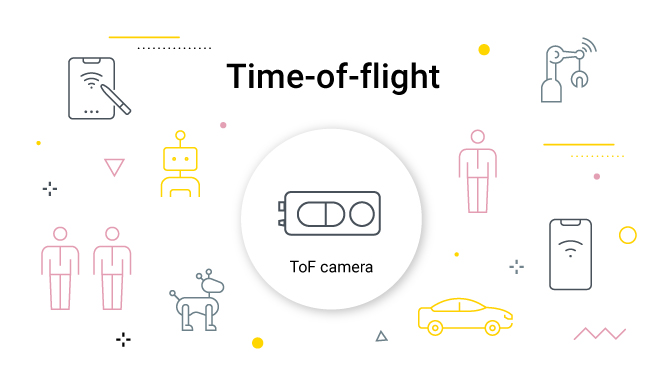
Table of Contents
Overview
3D cameras create a window into the real world for mechanical equipment, acting as an indispensable bridge and link in the automation process. They not only lead the wave of mechanical intelligence but also turn the dream of precise control into reality.
With the rapid advancement of automation technology, the requirements for 3D cameras have become increasingly stringent. What once was a pursuit of single precision has now evolved into the need for versatility, including system integration, high frame rates, resistance to light interference, support for multi-camera coexistence, and cost-effectiveness.
The biggest advantage of Time-of-Flight (ToF) cameras is versatility. ToF camera, with their excellent versatility, stand out among the many types of 3D cameras.
What is a Time-of-Flight Camera?
ToF technology uses active light detection to measure the distance by calculating the time it takes for photons to travel from the camera to the target object and back. ToF cameras can simultaneously measure both the intensity and distance of each pixel.
Direct ToF cameras (dToF) emit short light pulses lasting a few nanoseconds and measure the time it takes for some of the emitted light to return. Indirect ToF cameras (iToF) emit continuous modulated light and calculate the distance to an object by measuring the phase of the reflected light. [Learn more]
Advantages of ToF Cameras
In the context of automation, ToF technology offers several advantages:
High Speed
One of the significant advantages of Time-of-Flight cameras is their excellent performance in high-speed motion scenarios. Due to their ability to quickly scan the entire scene in a single exposure, they can output depth sensing data at up to 30 frames per second. This makes iToF cameras exceptionally suitable for high-speed or real-time applications requiring continuous and immediate feedback, such as mobile robots and people counting.
Accuracy
In terms of precision, although ToF cameras are not the highest precision 3D cameras, their accuracy can reach millimeter levels, which is sufficient for most industrial automation applications. Additionally, by not excessively pursuing ultra-high precision, manufacturers can save on procurement and integration costs.
Light Robustness
When discussing environmental adaptability, lighting conditions are a crucial aspect for 3D camera applications as they directly affect the accuracy of the output.
ToF cameras, as active 3D cameras, come with a built-in laser illumination system that allows them to function normally in any lighting condition, including complete darkness. This ensures continuous and accurate measurements.
At the other hand, Time-of-Flight (ToF) cameras perform exceptionally well even under strong light conditions. These cameras are designed to minimize the effects of intense light, allowing them to provide accurate measurements and clear images without being overwhelmed by bright light sources.
In practical terms, this means that ToF cameras can be used effectively in outdoor environments with strong sunlight or in indoor settings with powerful artificial lighting. Their ability to handle such lighting conditions ensures they can be relied upon for applications where precise depth sensing is critical, such as in autonomous vehicles, industrial automation, and augmented reality.
Compact and Lightweight
In terms of appearance, ToF cameras typically feature a highly compact and lightweight design due to the simplicity of their operating principles. They generally lack any complex moving parts, especially iToF cameras.
This characteristic can be expanded into a unique application advantage of being “superior both inside and out.” When used as finished cameras, Vzense’s various series are no larger than an adult’s palm, making them easy to equip on automated robots or forklifts. Additionally, the highest protection level of these cameras can reach IP67, allowing them to meet the operational requirements of harsh industrial environments.
As ToF modules, their dimensions can be even smaller, enabling easy embedding into various small or large devices, including smartphones.
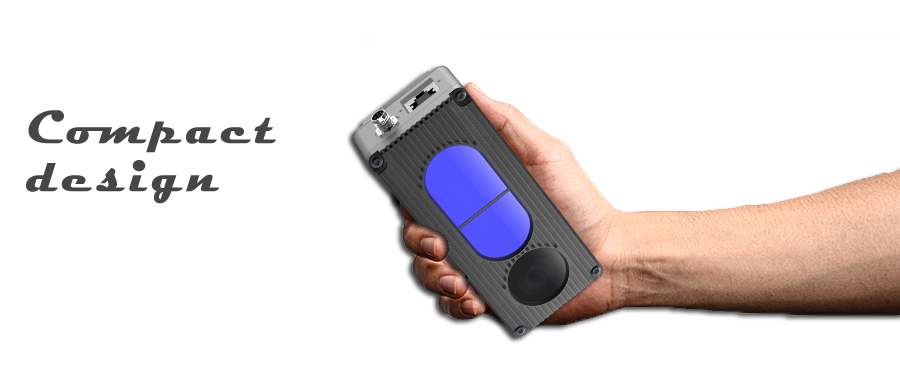
Support for Multi-Camera Coexistence
In addition to high frame rates, the support for multi-camera coexistence is another feature of ToF cameras, particularly important for automation applications such as mobile robots (AMR/AGV). While multi-camera coexistence is a strength of ToF cameras, not all of them can achieve unrestricted multi-camera coexistence.
Vzense’s pulse iToF camera NYX series, with ultra-high signal-to-noise ratio and advanced calibration techniques, can achieve unrestricted multi-camera coexistence. This allows mobile robots to work seamlessly and without interference in the same environment.
Cost-Effective
Finally, economic considerations are inevitable for large-scale universal applications. The manufacturing and procurement costs of ToF cameras are more affordable compared to other depth sensing technologies such as Structured Light Cameras and LiDAR sensors. This further broadens their application prospects in both consumer markets and industrial professional fields.
By leveraging these advantages, ToF technology enhances the efficiency and reliability of automated processes, contributing to smarter and more effective automation solutions.
Typical Applications of ToF Cameras
1. Pallet Recognition
Application Introduction: In logistics and warehousing, pallet recognition is a key step in the automation process. ToF cameras can quickly capture the 3D information of pallets, including their position, size, and shape, achieving precise identification.
ToF Advantages: ToF cameras are compact and lightweight, making them easy to integrate into various autonomous mobile robots or driverless forklifts without adding extra burden. The millimeter-level precision of ToF cameras is sufficient for pallet recognition while offering cost advantages that effectively control the overall cost of automated pallet recognition systems, facilitating wider application. ToF cameras are unaffected by lighting conditions and can operate stably in any lighting environment, ensuring the accuracy of pallet recognition. Vzense ToF cameras support unrestricted multi-camera coexistence, enabling multiple handling robots to work together smoothly in the same space. [Learn more]
2. Bin Picking
Application Introduction: Bin picking is another important task in logistics and warehousing, referring to the process of automated equipment dismantling or handling the stacked goods on pallets. The process involves arranging goods on pallets in a specific order for storage and transportation. Bin picking, in turn, involves taking the stacked goods off in individual or grouped units for subsequent sorting, packaging, or production processes.
ToF Advantages: ToF cameras feature high frame rates, capturing dynamic information of goods in real-time and ensuring that robots can respond quickly during depalletizing. In complex lighting conditions often found in depalletizing scenarios, ToF cameras remain unaffected and continuously provide accurate depth information. The compact design of ToF cameras is not limited by the size and shape of the space, allowing robots to move and operate more flexibly, enhancing the flexibility of depalletizing. [Learn more]
3. People Counting
Application Introduction: People counting involve monitoring and counting the number of people moving or staying within a specific area using various technologies. It is commonly used in commercial spaces, transportation hubs, public facilities, and tourist attractions to analyze traffic flow and behavior patterns, providing decision support. It is an important management tool in retail, transportation, and other fields.
ToF Advantages: The high frame rate of ToF cameras enables real-time pedestrian flow statistics, providing timely data support for managers. ToF cameras only capture depth information, protecting personal privacy as they do not involve individual images. The low cost of ToF cameras effectively controls the deployment and maintenance costs of pedestrian flow statistics systems. [Learn more]
4. Smart Factory Safety Fences
Application Introduction: Smart factory safety fences involve using advanced safety technology and equipment in smart factories to ensure safe production through real-time monitoring and analysis. They can monitor the surrounding environment in real-time and trigger alarms or stop dangerous operations when people or objects enter hazardous areas, significantly improving factory safety, protecting employees and equipment, and enhancing production continuity and efficiency.
ToF Advantages: ToF cameras can operate stably in any lighting conditions, even in “dark factories” without human supervision, ensuring continuous and reliable performance of the safety protection system. The high frame rate of ToF cameras allows the safety protection system to respond quickly to environmental changes, triggering alarms or taking safety measures in a timely manner. The compact design of ToF cameras makes the safety protection system lighter and more flexible, facilitating installation and deployment. [Learn more]
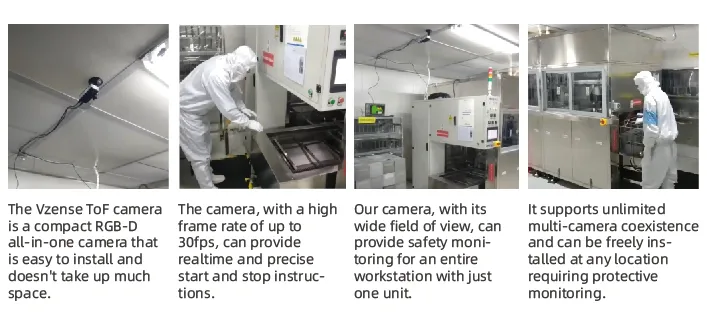
In summary, ToF cameras demonstrate unique versatility in pallet recognition, depalletizing, pedestrian flow statistics, and safety fences. Their compact and lightweight design, cost-effectiveness, resistance to light, and high frame rate make ToF cameras the preferred solution in these scenarios.
Vzense believes that Time-of-Flight technology is the trend in the evolution of future automation machine vision. Since 2017, we have focused on this technology, holding over 10 related patents and offering ToF cameras and modules that are well-received by the market and customers.
If you are interested in our ToF cameras, please leave a message on our website, send an email to vzense@goermicro.com, or follow our LinkedIn. We look forward to exploring more possibilities in industrial automation with you and maximizing the value of 3D data.