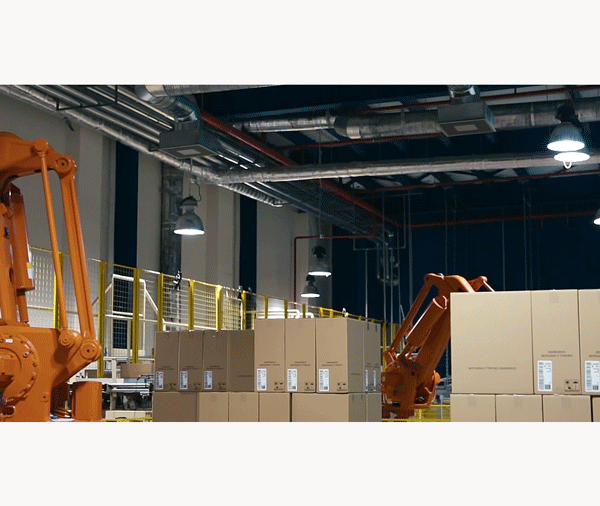
Challenges in Item Picking
Space Constraints
In material handling, optimizing space is vital for maintaining efficiency. However, as inventory grows, the complexity of shelf organization and logistics operations increases significantly.
Strict Accuracy Requirement
Objects with shiny or reflective surfaces can cause inaccuracies in depth measurements. In bin picking scenarios, items are often piled on top of each other, leading to occlusions.
Non-Standardized Packing
The lack of standardized packing and storage formats made robotic automation difficult, as it hindered the ability of robots to efficiently identify, handle, and organize diverse items.
Cost Concerns
The high cost of 3D sensors can significantly increase the overall expense of the system. This increase in cost is due to several factors, including the advanced technology and precision engineering involved.
Why ToF?
Item picking is a critical aspect of modern industrial automation, increasingly applied across various industries. However, traditional methods for achieving it have offered limited technological options. In the past, most systems used structured light technology, which often comes with high costs and unsatisfactory frame rates, making it less appealing.
This scenario changed with the emergence and mature application of Time-of-Flight (ToF) Camera. The use of ToF technology in item picking is a revolutionary breakthrough because it not only boasts technical advantages such as high frame rates and strong light resistance but also features a compact structure and low cost. This advancement not only improves the efficiency of item picking but also lowers the barrier to its adoption.
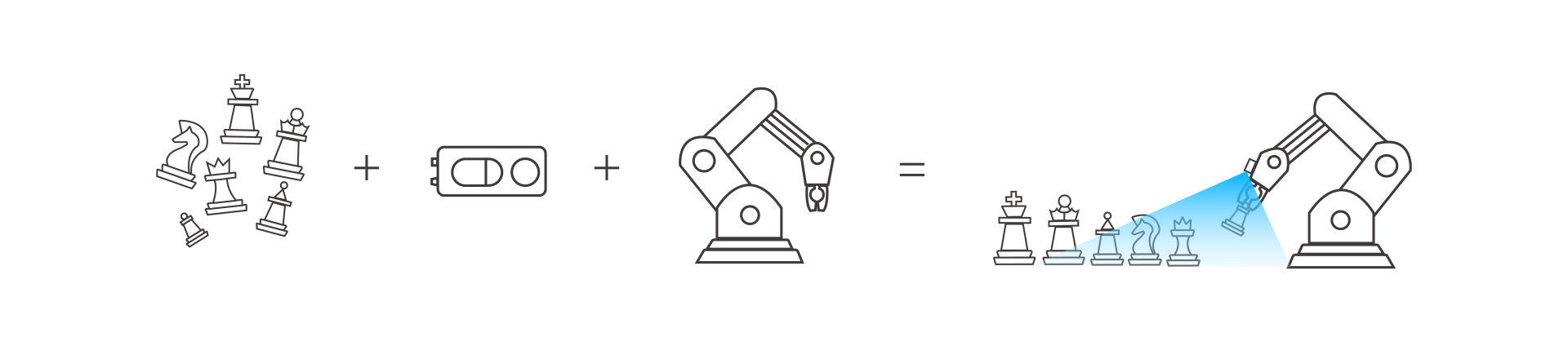

Higher Frame Rate

Strong Robustness against Ambient Light

Much More Compact

Lower Cost
Key Features of Vzense ToF Cameras in Items Picking
Vzense Time of Flight (ToF) cameras have extensive experience in the field of machine vision for item picking and enjoy widespread market recognition. We have established deep collaborations with renowned automation equipment companies in Japan, Australia, and other countries. So, how do Vzense ToF cameras tackle these significant challenges mentioned above? This stems from the unique advantages of our cameras, which are briefly outlined below.
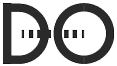
RGB-D Two in one Compact Design
Masterful compact design combined depth data
with RGB color data for color point cloud
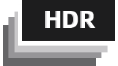
HDR Mode Supporting
HDR Mode combines multiple exposures in the phase
domain to provide accurate depth information
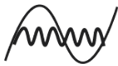
Dual Frequencies
The masterful combination of two different
frequencies helps to improves the overall accuracy
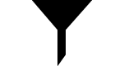
Filtering Tools
Filtering tools to fine tune and filter out
unwanted pointsin point cloud
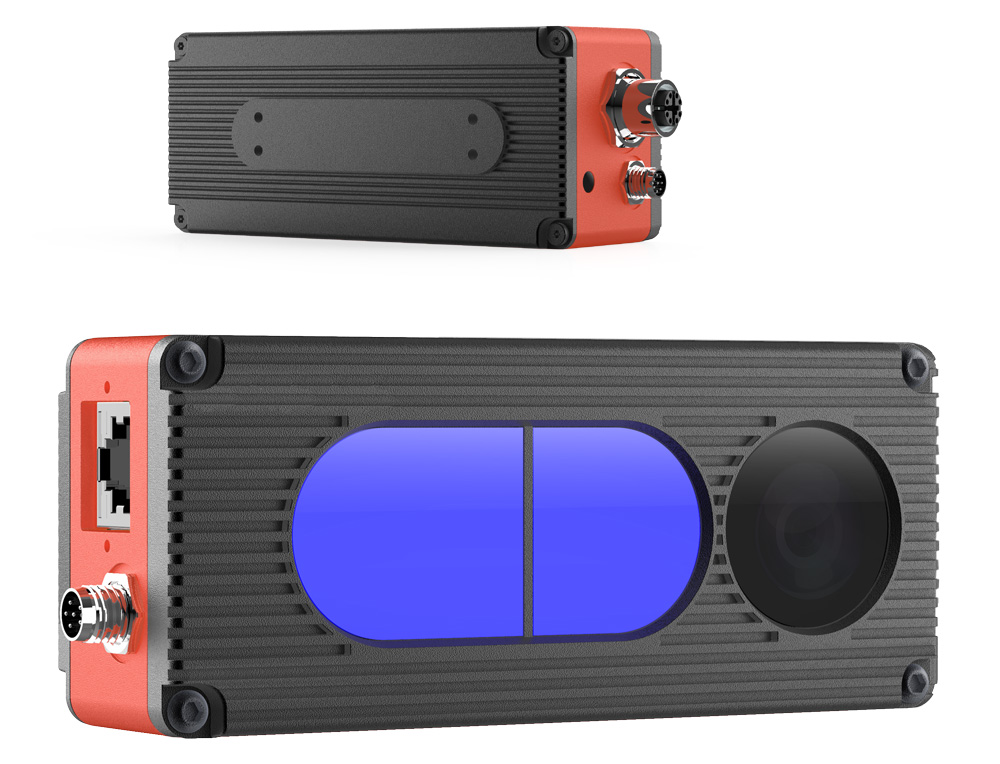
Handling All Reflectance Levels and Sizes with Ease
Its intuitive visual instructions enable workers of varying skill levels to perform tasks uniformly. Real-time decision-making, enabled by the 3D ToF camera, ensures operational accuracy without sacrificing speed. This adaptability and real-time feedback make the system a transformative tool in material handling, delivering unmatched accuracy and speed.
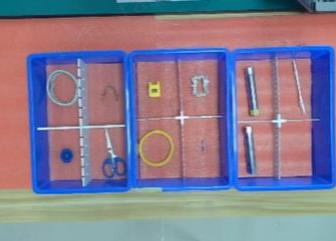
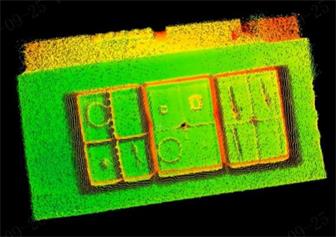
Vzense Cases
With numerous successful application cases in item picking, ranging from large to small items, we enable machines to handle them effortlessly.
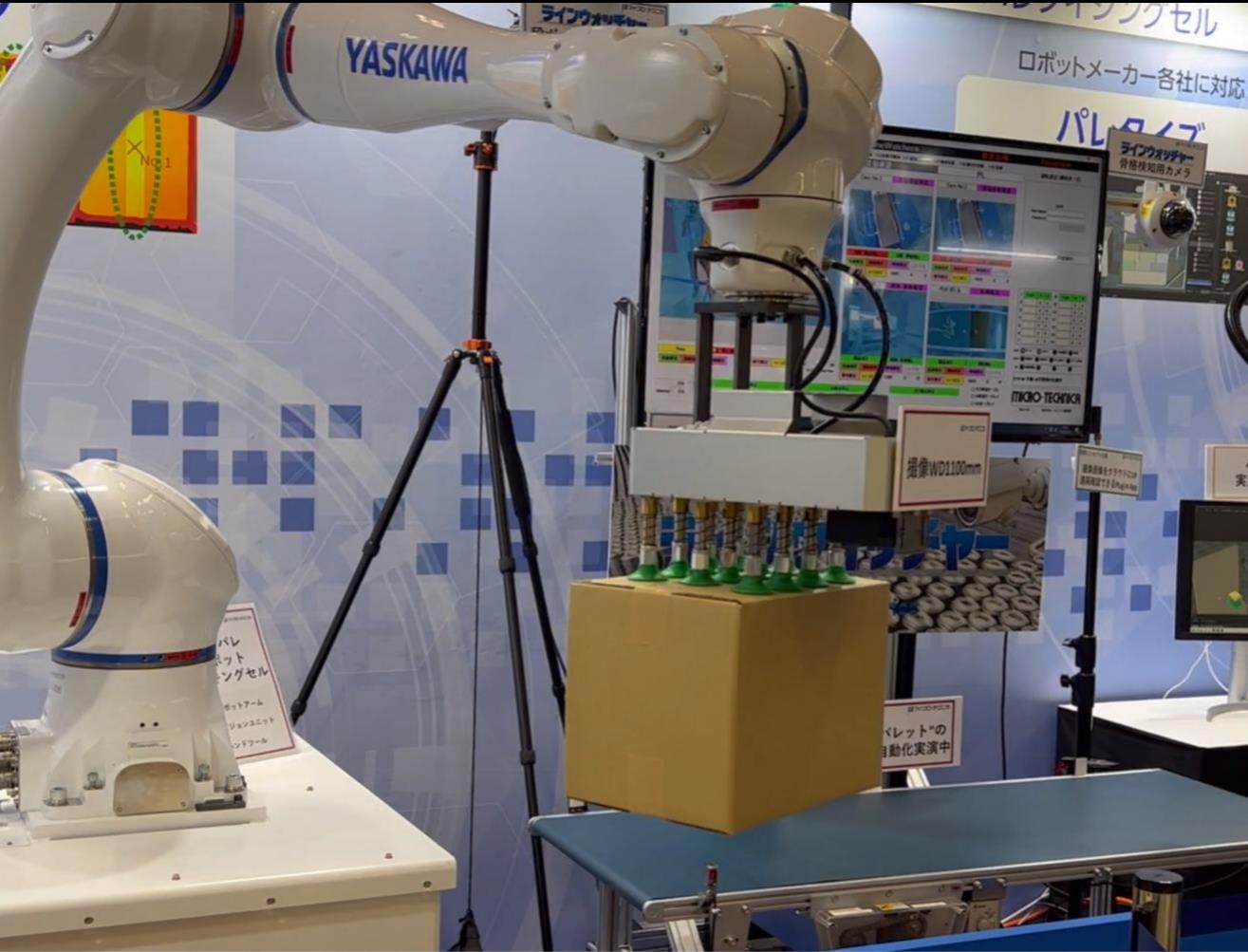
Bin Picking
Bin picking, also known as random bin picking, is a process in robotics and computer vision where a robot is tasked with picking up objects from a bin. These objects are often randomly placed and oriented, making the task challenging. The robot uses sensors, cameras, and grippers (such as suction or parallel grippers) to identify, pick, and place the objects. Vzense Time of Flight (ToF) cameras provide precise 3D depth information, enhancing the robot’s ability to accurately detect and handle items in various orientations and positions.
Smart Agriculture
Smart agriculture, also known as precision farming or digital agriculture, involves using advanced technologies like artificial intelligence (AI), the Internet of Things (IoT), robotics, and data analytics to optimize and improve agricultural practices. These technologies help farmers monitor and manage their crops and livestock more efficiently, leading to increased productivity, reduced environmental impact, and improved sustainability.
Vzense ToF cameras have extensive applications in smart agriculture and are highly praised by customers in Japan, the United States, and Australia.

Delta Robots
An industrial Spider Arm, also known as a delta robot, is a type of robotic arm widely used in manufacturing and automation. It features a base connected to jointed parallelograms, enabling precise and rapid movements. These robots are designed for high-speed picking and placing tasks, making them ideal for applications such as assembly lines, packaging, and sorting.
When equipped with Vzense iToF cameras, these robots gain enhanced precision in depth measurement and object detection. The ToF cameras provide accurate 3D depth data, allowing the robot to navigate complex environments, identify objects more accurately, and improve overall efficiency in tasks.
Discover More Applications
-
For AGV/AMR
Explore More -
People Counting
Explore More -
Item Picking
Explore More -
Automation
Explore More