The Time of Flight Camera: A Game Changer for Mobile Robots
Historically, RGB cameras have been the primary sensory component for industrial robots, capturing 2D images based on color information from a scene. However, 2D cameras have a significant limitation: they cannot directly measure distances without a calibration process, making them unsuitable for 3D applications like obstacle avoidance and navigation. Autonomous mobile robots (AMRs) require precise awareness of their constantly changing surroundings to navigate effectively, avoid obstacles, and accurately map their environment. This need has driven the development and adoption of Time-of-Flight (ToF) cameras, which have been in use since the late 1970s. Integrating ToF cameras into AMR guidance systems is a natural progression, enabling these robots to better navigate and interact with their environments.
Boosting AGV and AMR with ToF Camera
How ToF Cameras Take Perception A Step Further:
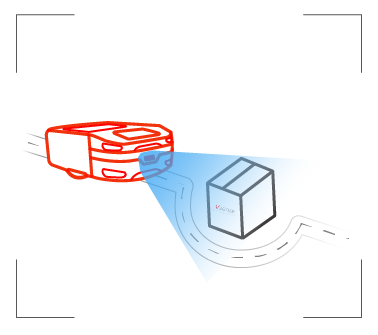
Obstacle Avoidance
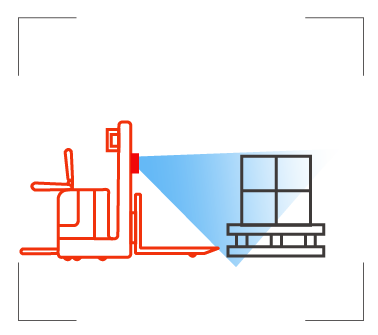
Pallet Recognizition
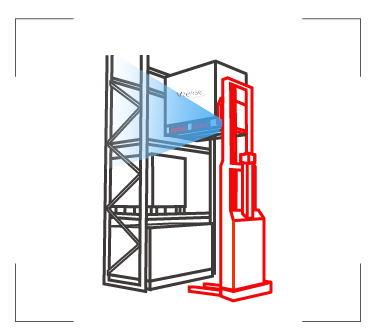
Load Handling
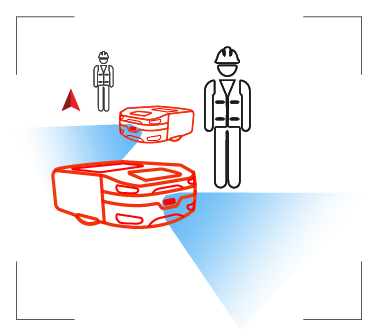
Navigation and Localization
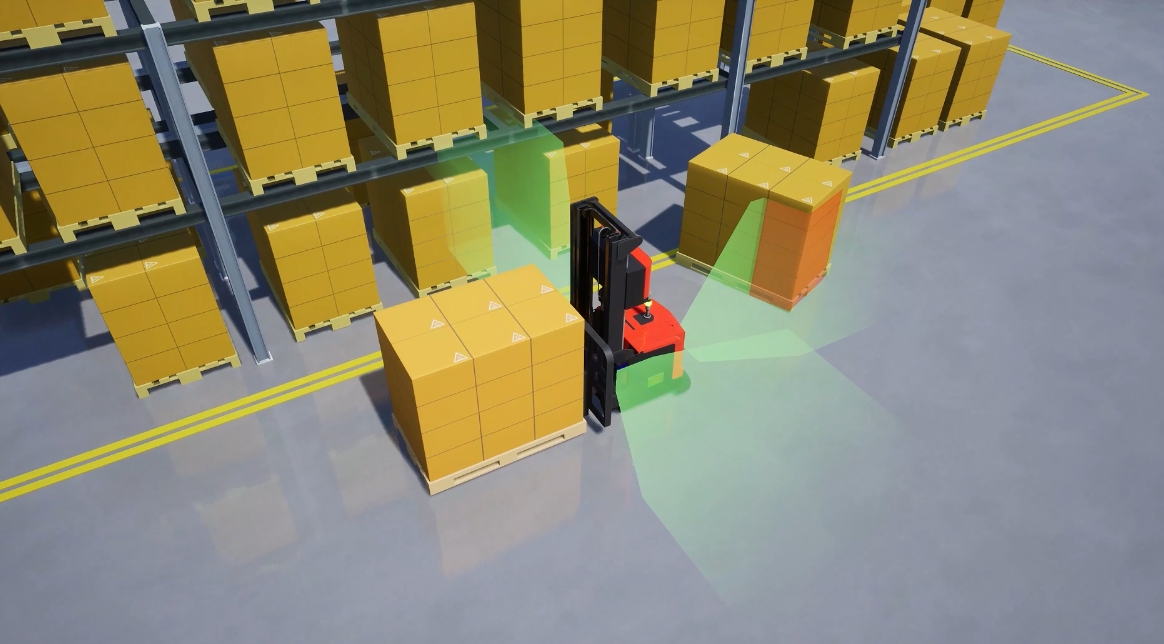
Simplifying Real-Time Obstacle Avoidance with Vzense’s User-Friendly ToF Cameras
The Vzense 3D Time-of-Flight (ToF) camera, with its wide field of view and instant flash imaging, enables high-precision 3D modeling of a mobile robot’s environment in real time. This capability remains unaffected by changes in the environment, making it ideal for supporting obstacle avoidance in mobile AGV robots. Additionally, this solution is cost-effective and less impacted by ambient light interference, offering reliable performance in various lighting conditions. Its ease of integration and robust performance make it a valuable asset for enhancing the efficiency and safety of automated systems across different industries.
Cutting-Edge Pallet Detection for Autonomous Forklifts
The Vzense ToF camera adopts a unique design that integrates an RGBD color camera and a depth camera into one highly integrated unit. This makes the product particularly suitable for empowering autonomous forklift operations in pallet detection. When the Vzense ToF camera assists an autonomous forklift in pallet detection, it first uses the RGB 2D color camera for precise identification of the target pallet. Then, it uses the depth image to measure the distance to the identified target, helping the autonomous forklift seamlessly and unobstructedly complete the recognition, positioning, lifting, and transportation of pallets of various materials and colors in different environments.
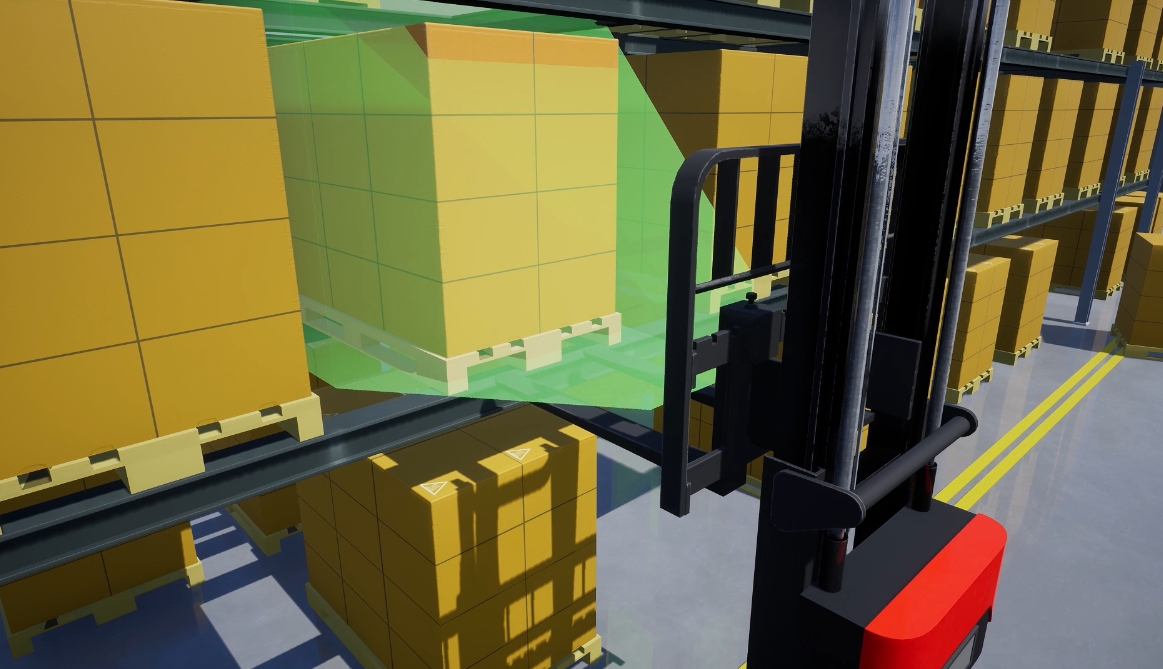
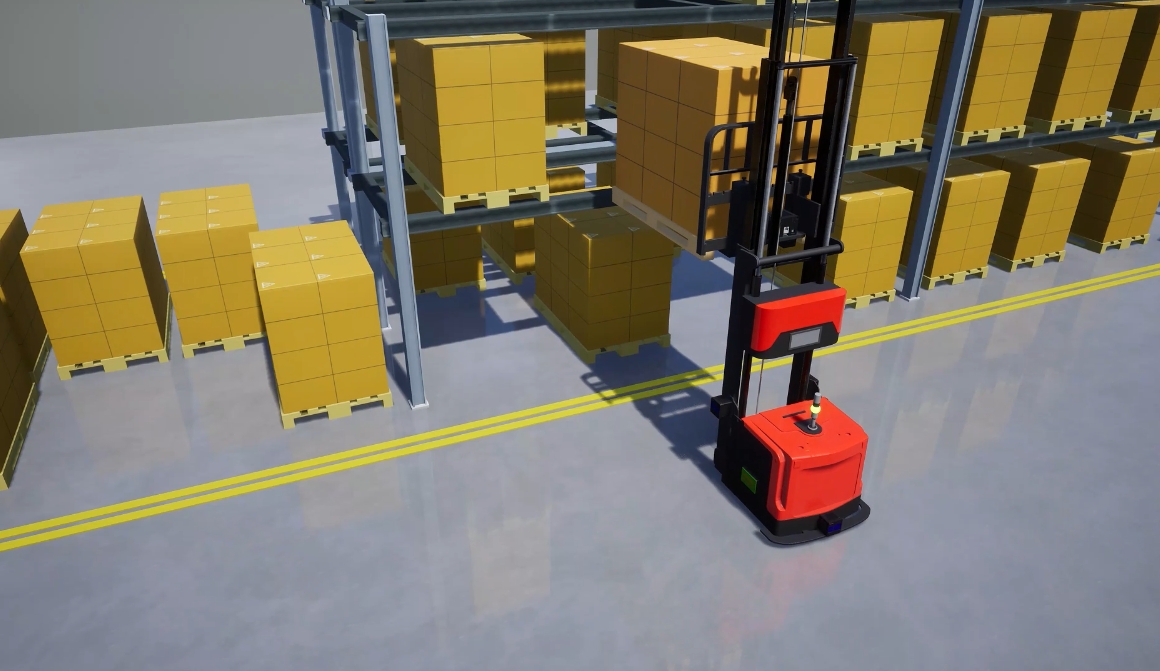
We Help Autonomous Forklifts Smoothly Tackle Load Handling Challenges
Load handling imposes significant demands on both automated vehicles and depth-sensing cameras. These 3D cameras must detect various surfaces and load geometries to ensure accurate identification and positioning of the load. Non-contact identification systems provide full traceability for goods transported by automated vehicles, ensuring efficient and reliable operations.
The Vzense iToF camera stands out in this regard. Its high accuracy ensures precise measurements and reliable load handling, while its ability to resist ambient light interference guarantees consistent performance in various lighting conditions. Additionally, the high frame rate allows for real-time detection and interaction, enabling automated vehicles to swiftly respond to dynamic environments.
Enhancing Autonomous Navigation with ToF Cameras
For an AGV to operate in unknown environments and execute autonomous tasks, it must adequately sense its surroundings. Vision sensors provide the necessary information for the AGV to perceive and avoid obstacles, enabling autonomous path planning. Therefore, the perception sensor is a key device for environmental awareness in intelligent mobile robots. The effectiveness of this sensor depends on three essential qualities: speed, compactness, and robustness. In addition to these qualities, the sensor must be reliable in various lighting conditions and able to process information quickly to facilitate real-time decision-making. This ensures that AGVs can navigate complex environments safely and efficiently.
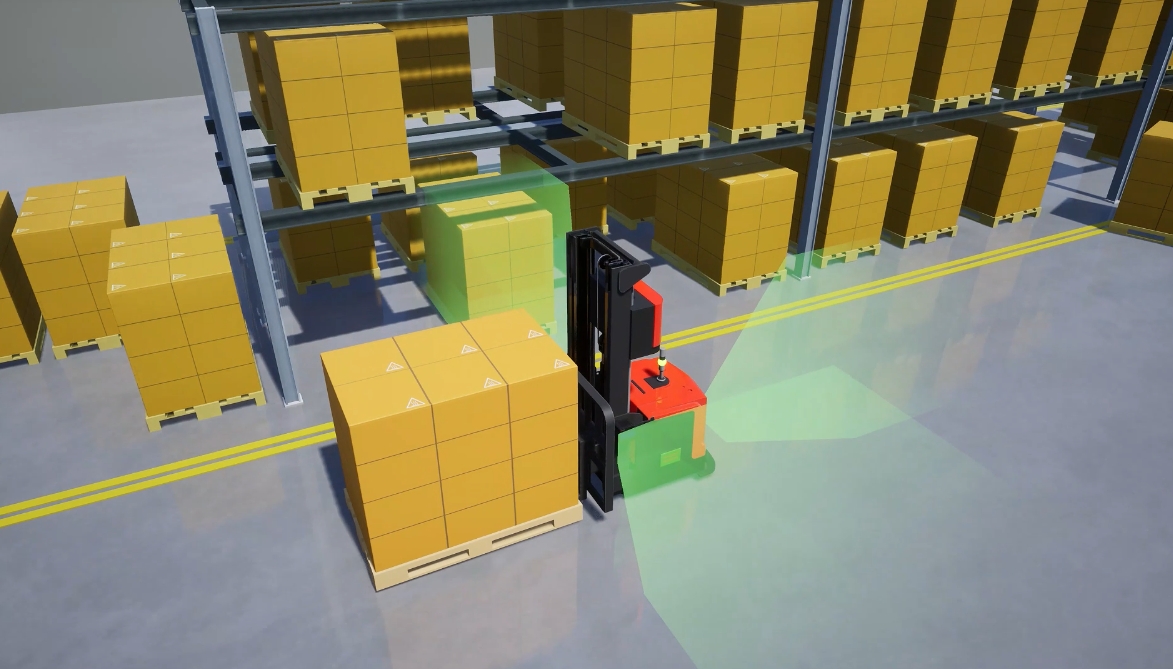
Irreplaceable Advantages of Vzense ToF Cameras
Advancing Perception with Vzense ToF Cameras
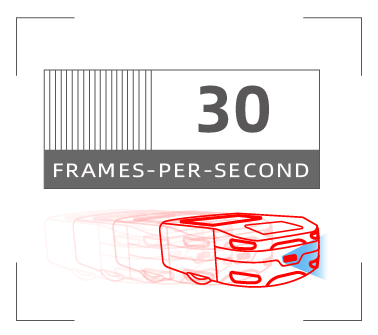
High Frame Rate
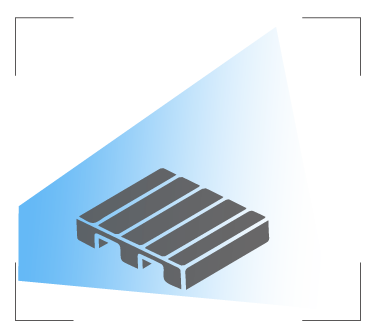
Optimized for Low Reflectance
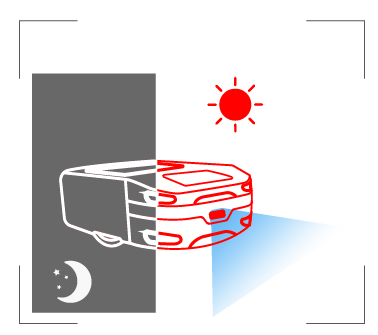
Robust Environmental Adaptability
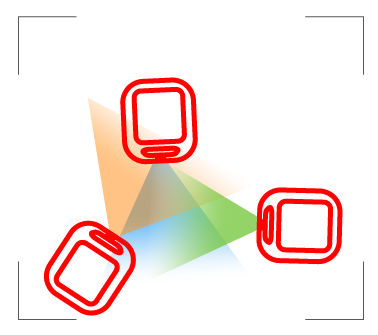
Seamless Coexistence Supporting
Moving at Will: 30fps Frame Rate
To detect and avoid obstacles swiftly, ensuring safety and efficiency, AGVs need high frame rate 3D depth sensing cameras. The high frame rate( up to 30fps) of Vzense iToF cameras enhances AGVs and AMRs by enabling real-time data processing. This allows quick and accurate responses to dynamic environments, efficient obstacle detection and avoidance, and precise localization. High frame rates also facilitate smooth navigation and enhance interaction with objects, ensuring accurate perception and manipulation. These capabilities make ToF cameras essential for improving the performance, safety, and efficiency of AGVs and AMRs in various environments. Additionally, the reliability of ToF cameras in diverse lighting conditions further enhances their operational effectiveness, making them indispensable in modern automated systems.
Optimized for Low Reflectance
In the use of AGVs, especially in the working environments of automated forklifts, it is often necessary to recognize various target objects with different surface materials and colors. These include low reflectivity objects such as black pallets, and high reflectivity objects like metal pallets or cargo wrapped in transparent plastic film. This requires the depth camera paired with the AGV to have strong recognition capabilities for both high and low reflectivity objects, particularly those with low reflectivity.
The Vzense 3D Time of Flight camera excels in this area. Utilizing a VCSEL laser emitter and a top-of-the-line ToF processing chip, it provides an ultra-high signal-to-noise ratio and accuracy, ensuring excellent performance in recognizing low reflectivity objects.

Great Ability to Capture Detailed Images in Scenes with Varying Lighting Conditions
As AGVs become more widely used in industrial applications, their usage scenarios have expanded from indoor environments to outdoor settings. This expansion places higher demands on the light resistance capabilities of the depth sensors paired with these vehicles. Vzense ToF cameras achieve great light resistance and robustness. We use VCSEL laser emitters, which emit light in the near-infrared spectrum to minimize interference from ambient light. High signal-to-noise ratios (SNR) help distinguish target reflections from background noise. This enables AGVs to swiftly detect obstacles, ensure smooth navigation, and accurately interact with objects.
The Reliable and Smooth Operation of the Cameras in Multi camera Systems
Traditional multi-camera systems often require physical synchronization or setting different modulation frequencies, which can be complex and demand high user proficiency. This is particularly challenging in high-speed scenarios like AGV/AMR, where synchronization and frequency adjustments are impractical, making it difficult to coordinate multiple cameras.
Vzense’s multi-camera coexistence technology eliminates the need for synchronization. Cameras can function independently without special configurations. Utilizing a proprietary avoidance algorithm and timing control, Vzense achieves unique, unrestricted multi-camera coexistence. This technology is particularly advantageous for AGV/AMR applications, ensuring reliable and efficient operation in complex environments.
How Is It Important for Depth Cameras Realizing Multi machines Coexistence
Discover More Applications
-
For AGV/AMR
Explore More -
People Counting
Explore More -
Item Picking
Explore More -
Automation
Explore More